Safety Best Practices
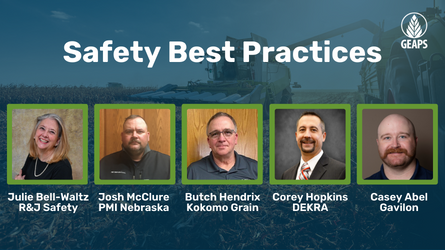
One of the great benefits of GEAPS membership is the ability to share information with industry colleagues.
Since the best way to learn something is straight from an expert, we reached out to a handful of GEAPS members who have committed their careers to making sure their colleagues go home each day. We asked them to dig into their proverbial safety toolboxes and share what they deem most important as we all work to make sure everyone stays safe on the job. Give it a read see what changes you could implement in your workdays to foster a safety culture in your workplace.
All GEAPS members, the experts we reached out to include Julie Bell-Waltz from R&J Safety, Josh McClure from PMI Nebraska, Butch Hendrix who serves as safety director for Kokomo Grain locations, Corey Hopkins with DEKRA and Casey Abel from Gavilon.
What is the best safety tip you’ve ever received?
Regardless of the job, never expect someone else to do what you yourself haven’t or won’t do. In other words: set the example, do what you expect others to do.
–JBW
Paperwork doesn’t make a safety program. Culture does. – JM
Overall, many times people aren’t sure if they should lockout/tagout, fill out entry permits, is it confined space or permit required confined space, wear respirators, goggles vs. safety glasses, etc. If you are not sure which way to go, go with the most stringent method. An example would be, if you’re not sure if the equipment should be locked out for what you are doing, go ahead and lock it out, and remove all doubt. Same with permits, if unsure, fill it out the permit to remove the doubt! – BH
Always challenge whether or not a task has to be done, or done the way “it has always been done.” Elimination is the most effective control in the hierarchy of controls. Sometimes we get in unnecessary routines, or do tasks simply because that’s the way it has always been done in the past. We must challenge those ideas. – CH
“Safety performance leads business performance”- Tom Krauss
Simply put, for an organization to be successful, safety and the wellbeing of its employees must be the #1 priority. An organization can preach safety as a priority, but they also must be willing to listen to the concerns of their employees, invest in their employee training and, most importantly, invest in safer systems and facilities. – CA
What is the most important thing people in the grain industry can do to keep themselves and their teams safe?
Always keep in mind “situational awareness.” Whether working on the farm or at the elevator, know what is going on around you. Every action has a reaction—what could go wrong? – JBW
Engaged leadership, constantly refining work processes and timely risk mitigation are the best way to ensure safe work practices. – JM
Team work, and helping others to operate safely. If you see something say something! – BH
Look at your policies and procedures as tools, not rules. There are some critical procedures out there (confined space entry, lockout tagout, fall protection, etc.) that get viewed as “rules.” If you actually study the procedures and follow them; they are truly tools that can prevent catastrophic outcomes. Use them accordingly. – CH
Build an effective safety culture, from top to bottom, starting with leadership. “Safety culture” can mean a lot of different things. In my mind, an effective safety culture starts with a focus on incidents involving a serious injury or fatality (SIF), or SIF potential. Employees must be willing to honestly report incidents and near misses without the threat of being reprimanded. Employees are not the problem makers; they are our most effective problem solvers. Increased reporting leads to increased solutions. Once reported, an organization should conduct extensive investigations that convey causal factor(s) that led to the incident. When key factors from an incident are identified, the focus should then shift toward how the organization betters its systems and/or facilities to effectively control the hazards. This not only applies to reacting to an incident, but also being proactive in identifying high risk operations and tackling hazards before an event occurs. Accepting that humans will make errors and building systems that allow that to happen without an injury is the only effective way to eliminate hazards in the workplace. We must shift from a “make do” to a “make right” mentality. This is done through eliminating, substituting, or engineering away from the hazard. Simply relying on employees to be flawless in their work, or demanding them be “safer,” will never lead to the results we desire. – CA
How do you stay up-to-date on safety best practices?
Stay up-to-date on safety best practices by talking to the guys doing the work. What is working for them? Meet and talk with equipment suppliers. What is the latest and greatest in safety equipment? Pay attention to recent OSHA citations in the grain industry. Serve on committees with safety peers. Read trade magazines like Grain Journal.- JBW
Experience, networking and working relationships with multiple vendors help me stay up to date. – JM
I’m a member of many organizations like GEAPS, NGFA, Agribusiness Council of Indiana, Indiana Risk Coordinators, Fire service, NFPA, and I also subscribe to many newsletters and email type newsletters. – BH
Continuous networking, newsletters, safety magazines/articles, memberships in safety associations, etc. – CH
This “new view” on safety isn’t necessarily new. Many industries, like the energy sector, shifted their focus toward SIF/p incidents years ago, and the results have been tremendous. Our industry must continue to learn from those who’ve done it right and have the results to prove it. Todd Conklin has been a huge voice in this “new view” on safety. His podcast “Pre-Accident Investigation” is full of great examples and insight from industry leaders. As far as the grain/feed industry, we must be willing to collaborate with one another and share practices that are working within our organizations. We may be business competitors, but we all have a common goal to send our employees home the way they showed up each day. Involvement in GEAPS is great platform for industry leaders to tackle our challenges around safety together. – CA
Anything else you want to mention?
It’s human nature is to think, “It’s not going to happen to me!” In our youth, we think we are invincible. As we age, we think we’ve been doing this for so long we must be right, we get complacent. Both extremes are hazardous to our wellbeing. No one gets up in the morning thinking they are going to do something stupid at work and die. Words of wisdom: you are NOT invincible. It is up to you to choose to do your job the safe way. Do not take shortcuts. – JBW
Nothing can substitute experience. If you don’t have it, ask someone who does. If you have it, mentor those who do not. – JM
I always try to involve our employees doing the day-to-day work in the development of policies and procedures. Many times, I also go out in the facility to work with employees as they are doing different tasks, to evaluate the hazards, along with reviewing the process for any policy updates. And, of course, to make sure it still within OSHA Standards. – BH
Safety has no quitting time. It’s a lifestyle, not a workplace thing. It’s important at work, at home, and on the road. – CH
Safety is a never-ending journey. We’ll never wake up one day and say, “we did it, we are 100 percent safe.” This creates complacency. We must continue to learn, evolve, and invest in safety systems as new challenges present themselves. Our industry is full of innovative minds working toward a common goal. Getting away from “the way we’ve always done it” and committing to continuously learning and system building is how we save lives in the future of on industry. – CA
You’ve read through what your peers had to say about staying safe, what do you have to add to the story? What are your safety tips and best practices? Please reach out to jessica@geaps.com to share your knowledge!